Applications
CERAMIC MEMBRANES IN TEXTILE INDUSTRY
Textile industries are rated as the most polluting among all industrial sectors taking into account both wastewater volume and composition.
Textile effluents produce colored wastewaters that are heavily polluted with dyes, textile auxiliaries and chemicals.
The wastewaters originating from dyeing processes are generally characterized by the high content of color caused by the dyestuffs, salts, chemical oxygen demand (COD) deriving from additives such as acetic acid, detergents and complexing agents, suspended solids including fibres, high temperature and broadly fluctuating pH.
In order to be able to reuse these effluents, membrane technologies have been proven as a viable alternative.
ENDURA, brand of Prism Johnson Ltd. is pleased to introduce Textile Effluent treatment with Ceramic Membranes.
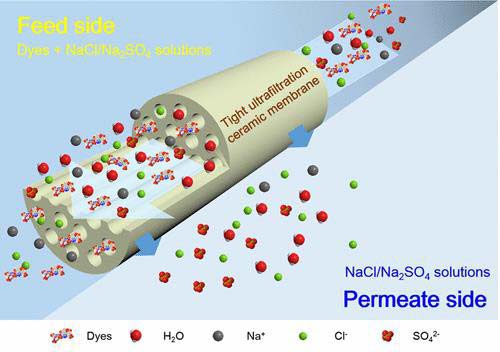
Compared with the organic membranes that are currently used in the industry, ceramic membranes have the following advantages:
- Good chemical stability, acid and alkali resistance and organic solvents, good oxidation resistance.
- High mechanical strength, no deformation under high pressure or large pressure difference, abrasion resistance, erosion resistance, high pressure back pressure can be used to regenerate the film.
- High temperature resistance. Generally it can be operated at 400°C. The maximum operating temperature is up to 800°C.
- The pore size distribution is narrow and the separation efficiency is high.
- The removal of suspended solids & organic matter is very good.
- The removal rate of insoluble dyes is more than 98% similarly removal rate of soluble dyes by adding some surfactants is more than 97%.
- Due to the strong permeability and good mechanical properties of the inorganic ceramic membrane, it can better separate the pollutants in the filter printing and dyeing wastewater.
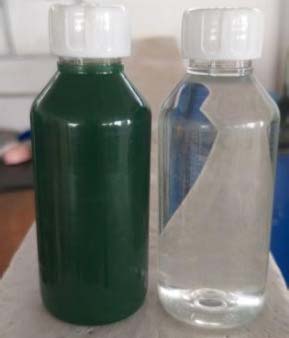
Result of Raw Printing & Clear Effluent
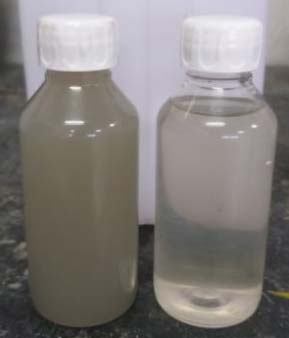
Result of Raw Bleaching & Clear Effluent